
Gear Shafts
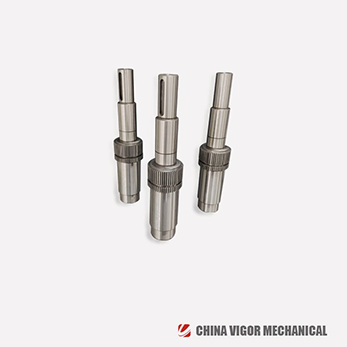
Production process: Turning, Milling, Drilling, Gear Shaping, Vacuum Heat treatment, Quenching, Grinding and 100% Inspection
Material: Alloy Steel, Stainless Steel (material grade as per customer’s request)
Surface roughness: Ra (μm) 0.4 & 0.8
Outer Diameter Tolerance: j5-j6
Inner Diameter Tolerance: E6
Coaxiality Tolerance: 0.02mm
Vigor produces high-accuracy gear shafts for Gear Reducer, Electric Motor & Brake Motor. Inspecting by both CMM and the full set of the specialized gauges for dimension linear tolerance and geometrical tolerance.
Detail Information
Application | Brake Motor / Gearbox |
Production process | Turning, Milling, Drilling, Gear Shaping, Vacuum Heat treatment, Quenching, Grinding, and 100% Inspection |
Material | Alloy Steel, Stainless Steel (material grade as per customer’s request) |
Surface roughness | Ra (μm) 0.4 & 0.8 |
Outer Diameter Tolerance | j5-j6 |
Inner Diameter Tolerance | E6 |
Coaxial Tolerance | 0.02mm |
Gear Shafts Display
![]() |
![]() |
![]() |
Gear Shaft Details Display
![]() |
![]() |
![]() |
Production Process
1. Heat Treatment Process of Gear Shafts
In the entire process of shafts machining, sufficient heat treatment procedures should be arranged to ensure the mechanical properties and machining accuracy of the gear shaft, and also improve the machinability of the workpiece.
1) Generally, normalizing is the first treatment after rough shafts are forged to relieve internal stress, refine the grains, and improve the machinability.
2) Arrange Q+T treatment after rough machining. Through rough turning, drilling, and other processes, most of the machining allowance of the gear shaft is cut off. In this stage, the cutting force and heat are very large. Under the action of force and heat, the shaft will have large internal stress. The stress can be relieved by Q+T treatment, instead of aging treatment, and the required toughness can also be obtained simultaneously.
3) At this stage, except for the machining allowance of important surfaces, other surfaces and dimensions have reached the design requirements. At this time, arrange local quenching treatment on teeth and another required surface to meet the hardness requirements and ensure the wear resistance of these surfaces. The subsequent final machining process will relieve the quenching deformation.
2. Machining Process of Gear Shafts
The machining process sequence is based on the principle of confirming the datum surface first, machining the general accuracy surface prior to the high accuracy surface, and machining main sizes in priority.
In the gear shaft machining process, heat treatment is the demarcation. Rough machining prior to QT treatment, semi-finish machining prior to quenching, and finish machining behind quenching. Arrange the finish machining process at the final stage to avoid the main surface accuracy being affected by the stress during other surface processing.
Product Package
When arranging the gear shaft process, the following points should also be noted.
(1) Because the tooth profile machining is relatively a large workload and difficult process content, the tooth profile rough machining should be arranged behind the semi-finish machining of the excircle to improve the accuracy. The tooth profile finishing should be arranged behind all the external surfaces machining completed, in order to relieve the heat treatment deformation caused by the tooth partial quenching.
(2) Machining the bigger excircle prior to smaller excircles to ensure the shaft’s rigidity in the production processes.
(3) The other processing, such as the keyway of the gear shaft should generally be arranged behind the excircle finish turning or rough grinding, but before the finish grinding. If the keyway is milled before finish turning, then there will be the vibration of intermittent cutting when finish machining. It will affect the processing quality, and keyway sizes and also easy to damage the tool.
hotTags : Gear Shafts,China, suppliers, manufacturers, factory, foundry, customized, buy, quotation, low price, high quality, high accuracy, high performance, free sample,accurate,OEM.