
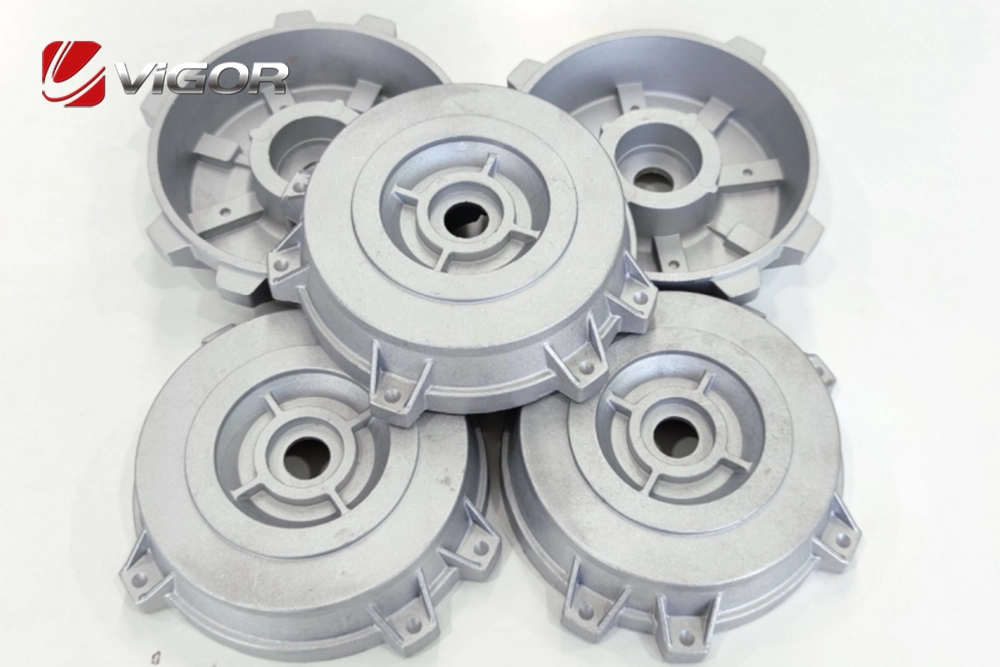
The commonly used materials in die-casting processes mainly include non-ferrous metals such as aluminum, zinc, magnesium, and copper, as well as their alloys. These materials hold significant importance in the die-casting field due to their unique physical and chemical properties.
2025-03-26 13:24:55
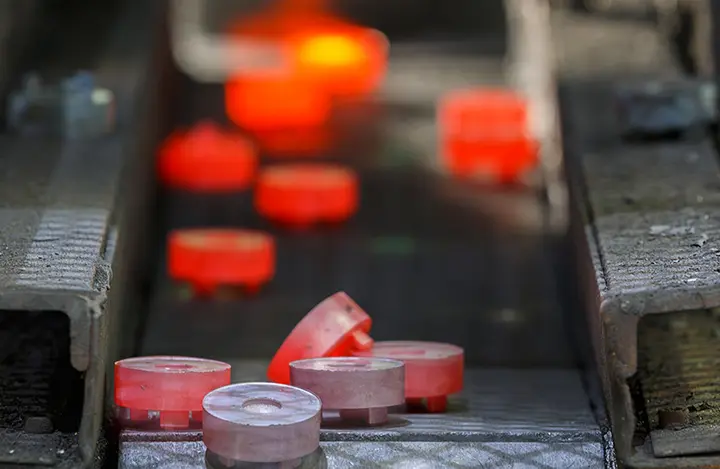
Heat treatment methods have a direct and significant impact on the recrystallization process of metallic materials. Recrystallization is an important process in which metallic materials, during heat treatment, eliminate dislocations and crystal defects generated during cold or hot working through the re-nucleation and growth of grains, thereby restoring the material's plasticity and toughness. The following are several common heat treatment methods and their specific effects on the recrystallization process of metallic materials:
2025-03-26 13:17:21
_1742966068596.webp)
The core of the chemical reaction formation: During the smelting of the molten iron and the subsequent processing, the magnesium, rare earth and other elements in the spheroidizing agent will undergo chemical reactions with sulfur, oxygen and other elements in the molten iron, generating sulfides and oxides. These compounds, such as MgS, MgO, RE2O3, etc., are initially small in size and serve as substrates for the nucleation of graphite, that is, the spheroidization core.
2025-03-26 13:15:24
The strength of resin sand is often classified into room temperature strength and high-temperature strength. Room temperature strength is further divided into initial strength and final strength. Initial strength refers to the strength of the molding sand immediately after mixing, while final strength refers to the strength of the molding sand after 24 hours.
2025-03-26 11:23:15
Carbon
Atomic number: 6
Density (20°C): 2.3 g/cm³
Atomic weight: 12.01
Melting point: > 3550°C (6422°F)
Boiling point: 4827°C (8721°F)
2025-03-26 11:21:16
To determine whether ductile iron is prone to porosity, the following aspects can be considered:
2025-03-25 18:06:59
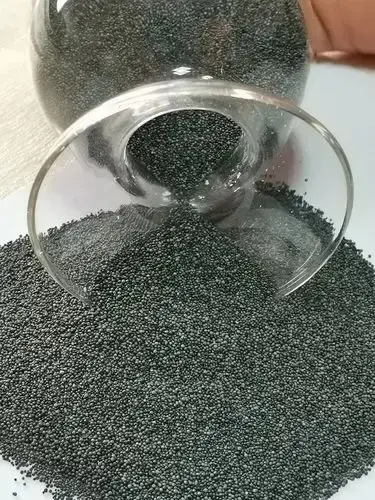
Baozhu sand is a green and environmentally friendly casting sand, also known as electrically fused ceramsite, ceramsite sand, or jewelry sand. Its scientific name is "fused ceramic sand".
Raw Materials and Manufacturing Process
Baozhu sand is made from high-quality bauxite as the raw material and processed through calcination, electric melting, granulation, and screening to produce spherical refractory material particles.
2025-03-25 18:06:03
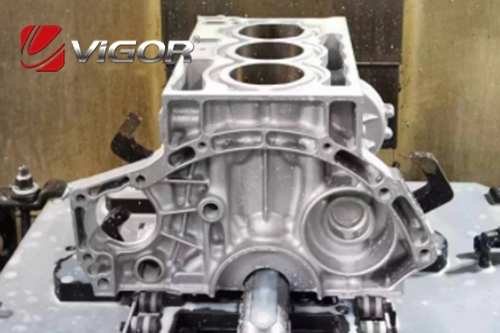
Hot chamber die casting is a time-honored die casting technique characterized by the direct immersion of the injection mechanism into the molten metal. This process is suitable for low-melting-point metals such as zinc, tin, and lead alloys.
2025-03-21 18:09:08
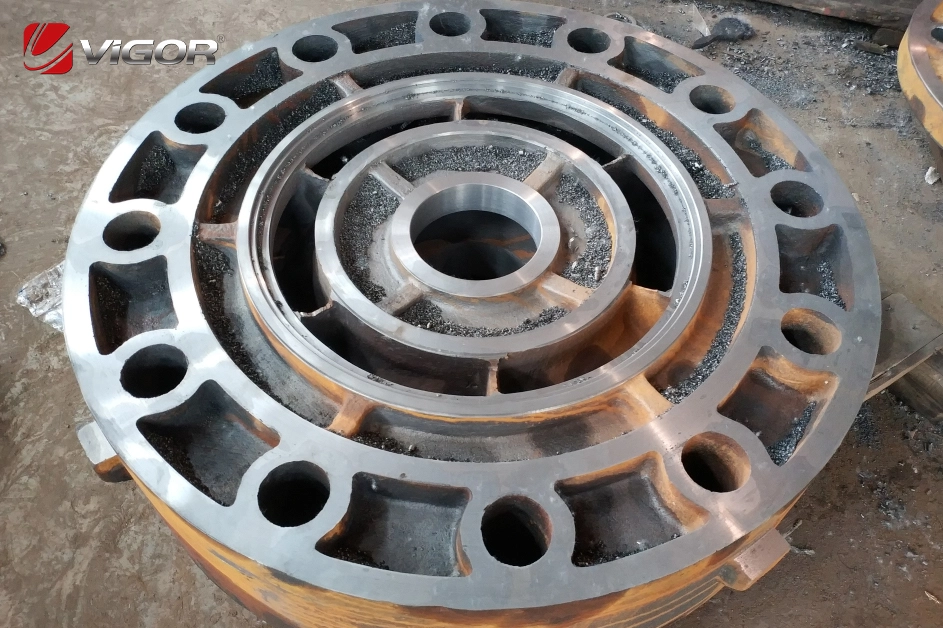
The type, properties, and moisture content of the resin can have an impact. For instance, furan resin with a relatively high moisture content will inhibit the condensation reaction, slow down the hardening speed, and extend the working life and molding time. If the pH value of the resin is too high, it will consume more curing agent, also causing the hardening process to slow down.
2025-03-21 18:03:44
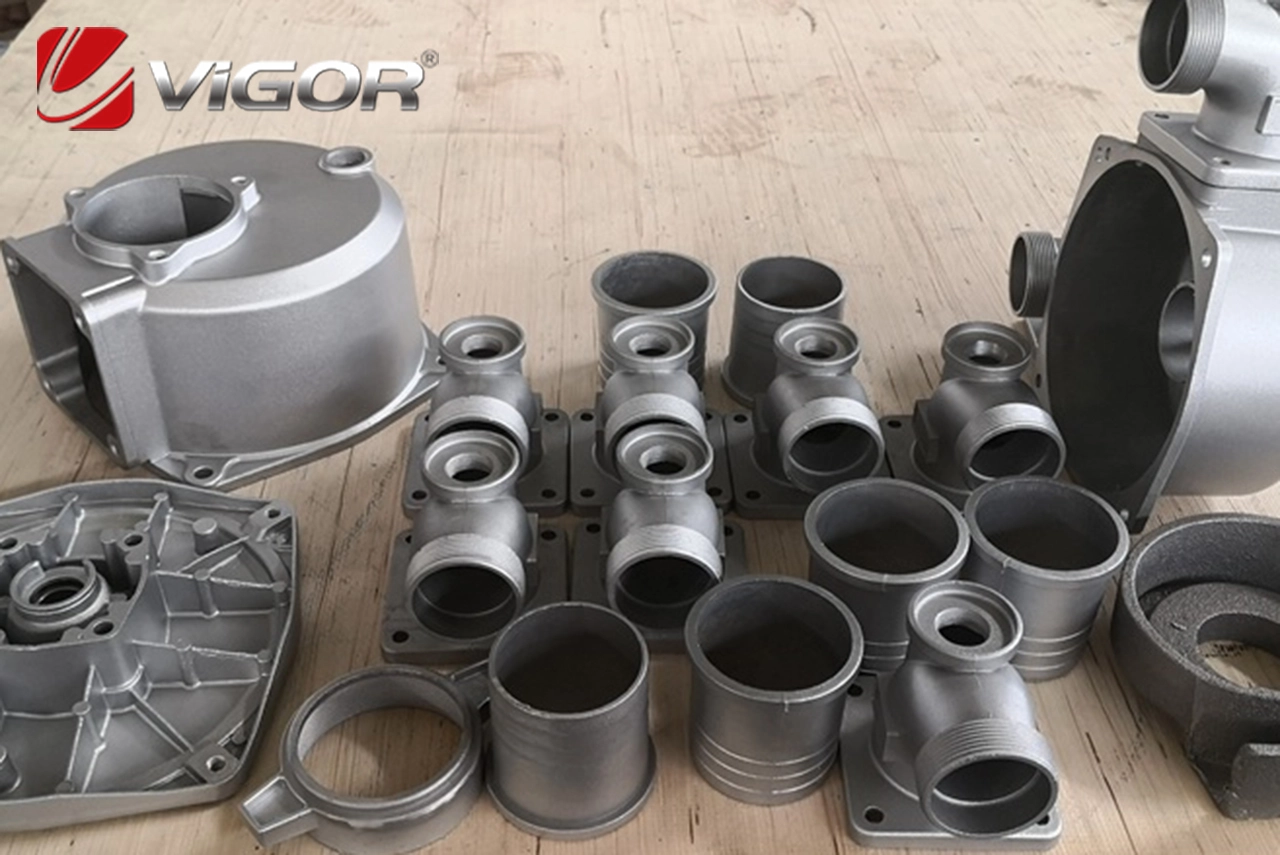
Mold design is a crucial step in the die-casting process, directly influencing the quality of the castings and production efficiency. It requires comprehensive consideration of the casting's shape, size, functional requirements, as well as the fluidity and solidification characteristics of the alloy.
Mold material selection: Commonly used mold materials include steel and aluminum alloys, among which H13 steel is widely employed due to its excellent thermal stability and wear resistance. The choice of mold material should be based on the production volume of the castings, the type of alloy, and cost-benefit analysis.
2025-03-19 18:23:02
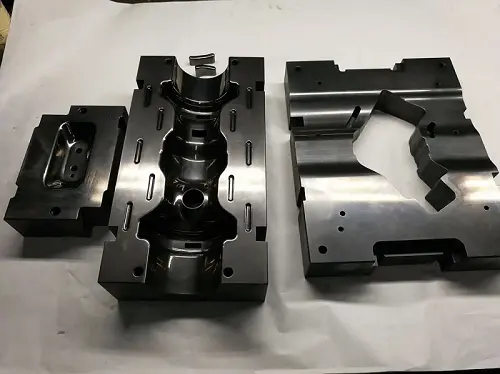
The functions and characteristics of the inner cavity coating of molds and various coatings are as follows:
2025-03-19 18:22:07
Cracks in castings are common problems in the casting manufacturing process. The causes are complex and diverse, mainly including internal defects in the casting, temperature stress, pressure stress, unreasonable casting design, and improper cooling measures.
2025-03-19 18:18:23
272