
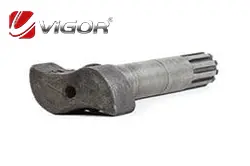
A worn-out brake camshaft is a significant concern for vehicles and machinery relying on braking systems. Symptoms of a failing brake camshaft include unusual noises during braking, uneven braking performance, difficulty in applying brakes, and excessive wear on brake components. Ignoring these signs can lead to serious safety risks and costly repairs. This guide will help you identify the common symptoms of a worn-out brake camshaft, understand its causes, and outline preventive measures to extend its lifespan.
2025-02-19 09:29:24
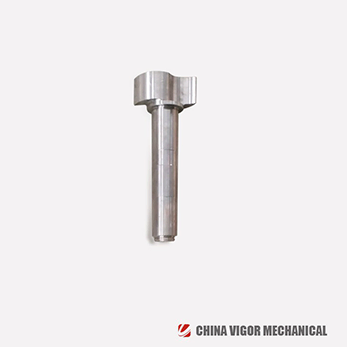
Precision die forging is revolutionizing the production of brake camshafts, offering unparalleled quality, performance, and durability. Brake camshafts play a critical role in ensuring the safety and efficiency of heavy-duty vehicles, making their precision and reliability essential. Through advanced die-forging techniques, manufacturers can produce brake camshafts with superior structural integrity, reduced material waste, and optimized performance for the most demanding applications. With VIGOR INNO-TECH's 18+ years of expertise in castings and forgings, we deliver excellence in brake camshaft production, ensuring unmatched quality and efficiency for our global customers.
2025-02-19 09:29:14
_1740034814477.webp)
The brake camshaft plays a critical role in ensuring proper brake adjustment by transferring the force from the brake pedal to the brake shoes or pads. This component rotates when the brake pedal is pressed, causing the brake shoes to press against the drum or rotor, creating the friction necessary to slow down or stop a vehicle. If a brake camshaft is worn, misaligned, or damaged, it can lead to uneven braking, reduced efficiency, and even unsafe driving conditions. Ensuring the brake camshaft is in optimal condition is key to maintaining precise brake adjustments and overall vehicle safety.
2025-02-19 09:29:05
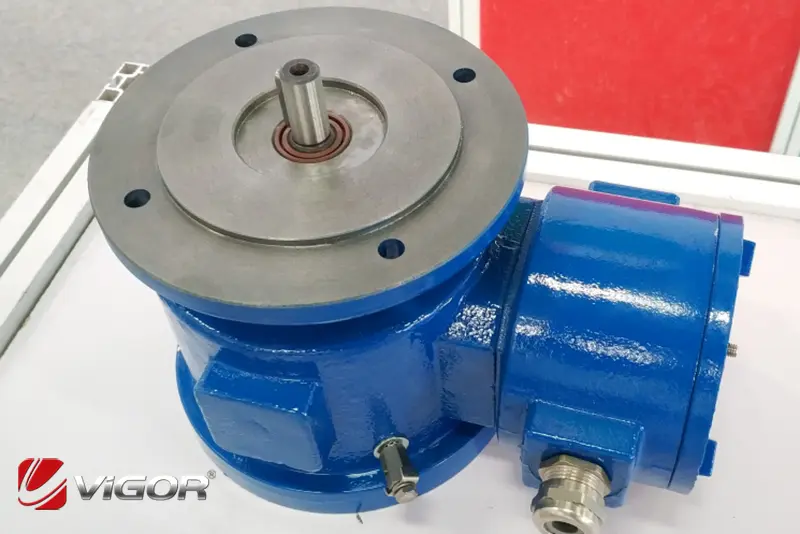
Electric motor brakes can be classified into various types based on their working principles and application scenarios, each with its own unique characteristics. The following are some common types of electric motor brakes and their features:
2025-02-18 17:41:13
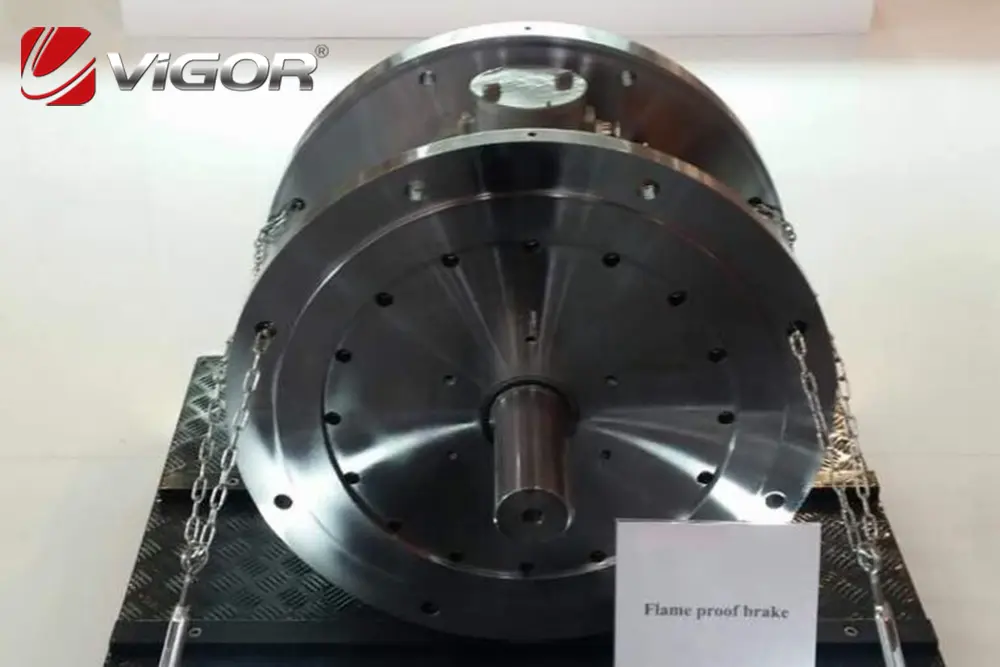
The design of disc brakes is a complex and meticulous process, involving precise calculation and optimization of multiple key parameters. Firstly, the diameter and thickness of the brake disc need to be carefully designed based on the load and braking requirements of the equipment to ensure sufficient braking force and heat dissipation performance. The inner and outer radii and area of the friction lining also need to be accurately calculated to ensure full contact with the brake disc and uniform wear. In addition, the pressure distribution of the brake wheel cylinder is also a key point in the design, directly affecting the braking effect and stability. There are various types of disc brakes, mainly divided into two categories based on the structure of the positioning elements in the friction pair: caliper disc brakes and full disc brakes. Among caliper disc brakes, fixed caliper disc brakes are widely used in light-load equipment due to their simple structure and easy maintenance, while floating caliper disc brakes are more commonly used in heavy-load equipment due to their good braking effect and strong adaptability. Full disc brakes provide a stronger and more stable braking effect when all the friction surfaces of the discs are in full contact. According to different usage environments and requirements, industrial disc brakes can be further classified into various types such as normally open, normally closed, and adjustable types to meet the braking needs of different working conditions.
2025-02-18 17:31:35
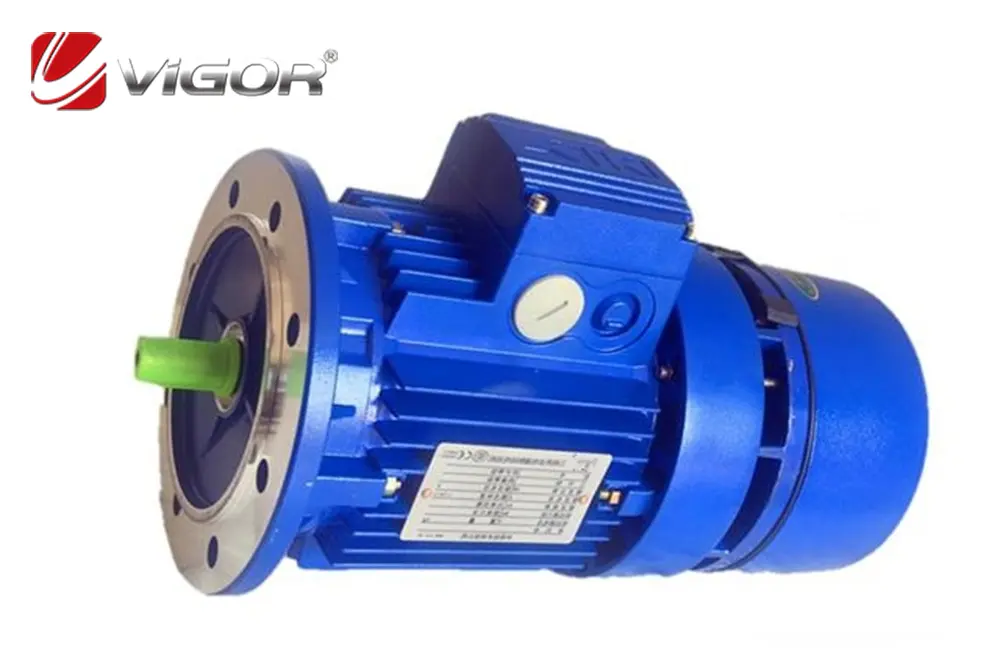
Brake motor housings are an important component of motor structures and are mainly divided into two categories: motor housings and brake housings. Motor housings typically use high-strength, lightweight aluminum alloy materials, which not only have good thermal conductivity but also effectively reduce the overall weight and improve the motor's operating efficiency. Brake housings, on the other hand, are mostly made of wear-resistant and high-temperature-resistant cast iron materials to ensure they can withstand significant mechanical stress during frequent braking. Additionally, these housings have a high protection level, such as IP54 or IP55, effectively preventing dust and moisture from entering and ensuring stable motor operation in harsh environments.
2025-02-18 17:24:04
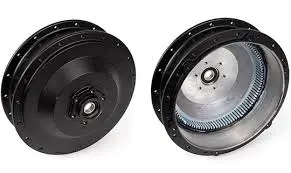
2025-02-17 09:51:22
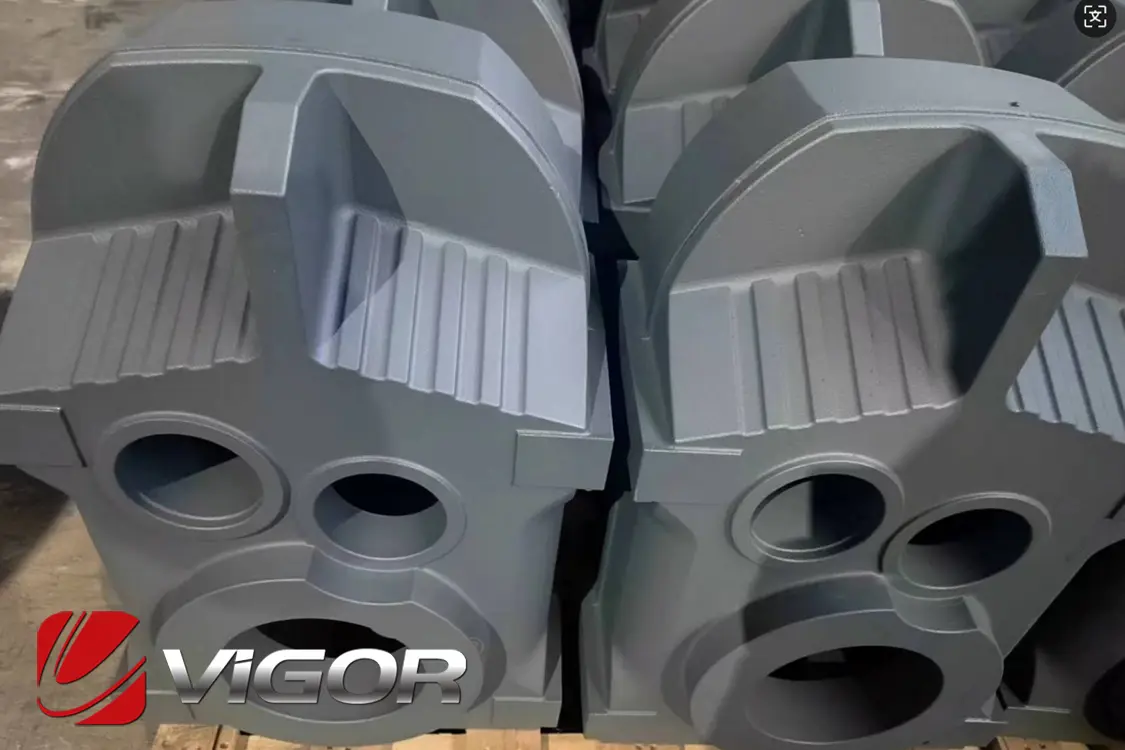
The types of reducer housings are diverse, and the specific choice often depends on the model of the reducer and the application scenario. Its core function is to protect the internal precise transmission components, effectively preventing dust, moisture, and other impurities from entering, thereby ensuring the stable operation of the reducer. At the same time, the housing also plays an important structural support role, ensuring the mechanical strength and stability of the entire reducer in complex working environments.
2025-02-14 17:13:51
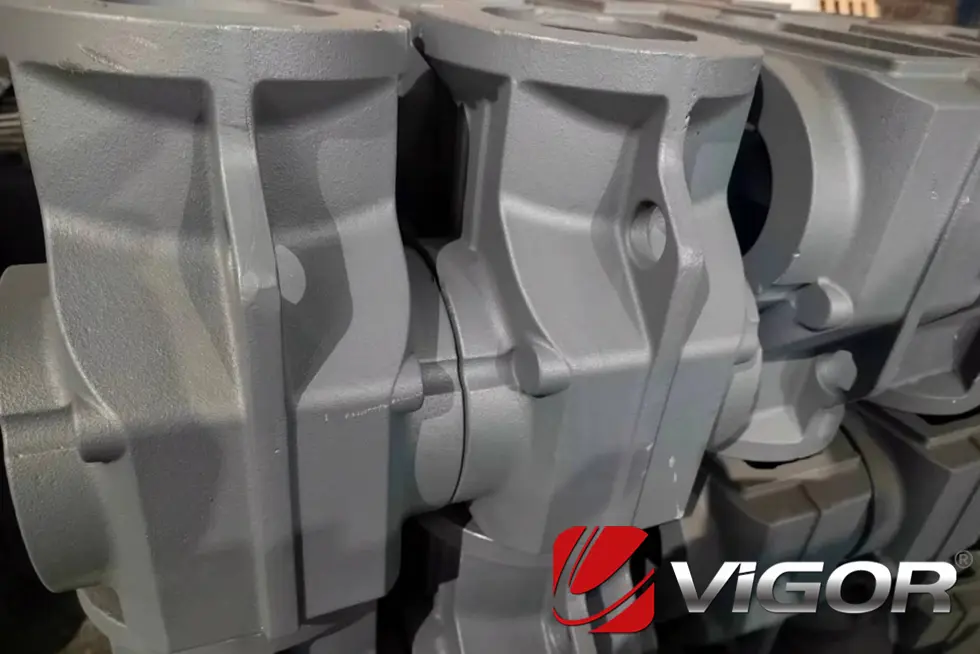
To enhance the service life of the reducer housing and carry out proper maintenance, the following aspects can be considered to ensure the stability and efficiency of the reducer during long-term operation.
I. Methods to Increase the Service Life of Reducer Housing
1. Select High-Quality Materials: When manufacturing the reducer housing, choosing materials with high strength, corrosion resistance, and wear resistance is crucial. High-quality alloy steel or high-grade cast iron not only have excellent mechanical properties but also remain stable in harsh environments. By selecting the right materials, the fatigue resistance and aging resistance of the housing can be fundamentally enhanced, ensuring it does not crack or deform easily during long-term use.
2025-02-14 17:10:36
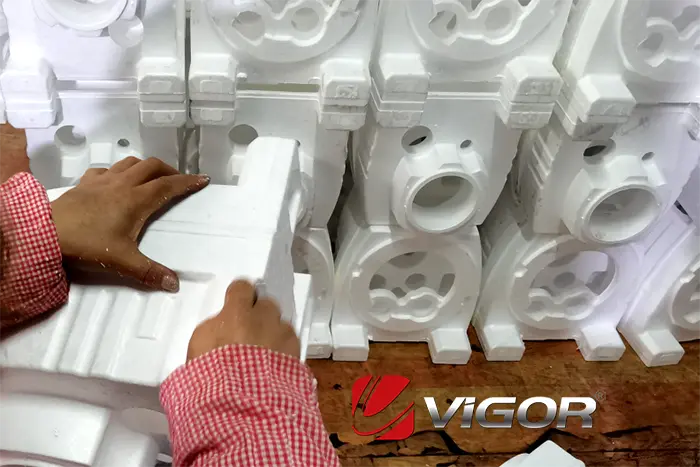
Casting process:Casting is one of the important processes in the production of reducer housings, especially for those with complex shapes and large sizes. During the casting process, parameters such as casting temperature, pouring speed, and cooling time need to be strictly controlled to ensure the quality and performance of the housing. Specifically, the selection of casting temperature should take into account the melting point and fluidity of the material; too high or too low a temperature will affect the quality of the casting. The control of pouring speed directly relates to the density and surface quality of the casting interior; too fast a speed may cause porosity and slag inclusion, while too slow may result in cold laps. The length of cooling time affects the crystalline structure and stress distribution of the casting, and needs to be optimized based on the specific material and casting structure. Through high-quality casting processes, uniform-structured and mechanically sound shell blanks can be obtained, laying a solid foundation for subsequent processing.
2025-02-14 17:03:50
131