
2025-02-13 15:28:17
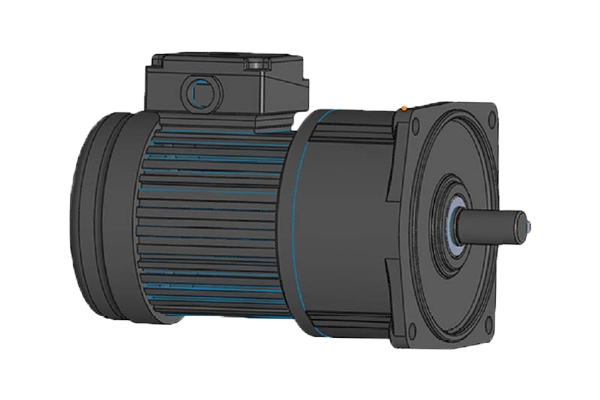
Motor brake housings are typically made from durable materials that can withstand high stress, heat, and environmental factors. The most common materials used for brake motor housings include ductile iron, cast iron, aluminum alloys, and stainless steel. These materials provide the necessary strength, corrosion resistance, and heat tolerance required in demanding industrial applications. Ductile iron, in particular, is highly favored for its ability to absorb shock and resist wear, making it ideal for explosion-proof brake motor and flame-proof brake motor housings. Each material has its own benefits, and the choice depends on factors such as the operating environment, load requirements, and cost considerations.
2025-02-12 09:18:22
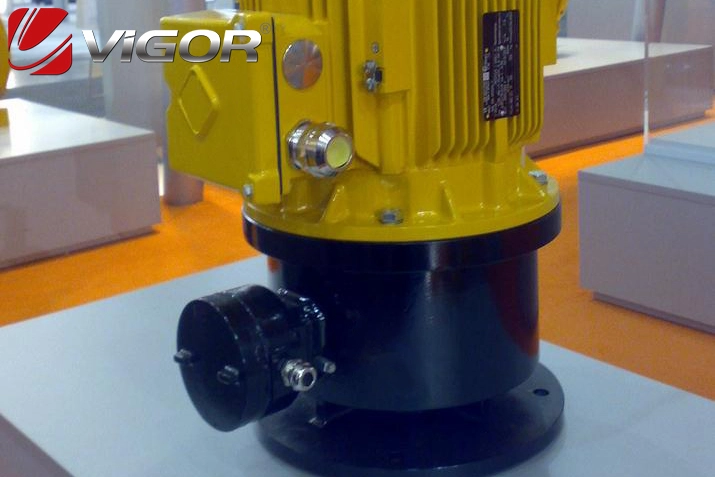
The manufacturing process behind motor brake housing is a highly specialized and precise operation that requires advanced techniques to ensure safety, durability, and performance. Brake motor housings - often used in explosion-proof or flame-proof motors - are crucial components that protect the internal brake system from external environmental factors, such as heat, pressure, and potentially hazardous conditions. The process of producing these housings typically involves resin sand casting, a method that ensures high-quality, durable parts. This article delves into how motor brake housing is manufactured, the necessary steps involved, and why selecting the right method is essential for optimizing performance and efficiency.
2025-02-12 09:18:14
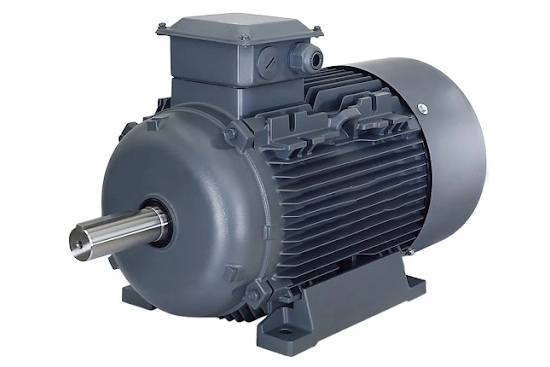
The motor brake housing is a critical component in various industries, offering safety and reliability in harsh environments where explosion risks are present. Designed to contain any sparks generated during motor operation, these housings ensure that brake motors function safely in industries such as coal mining, oil and gas, petrochemicals, textiles, and metallurgy. This article explores the essential role of motor brake housings across different sectors and how they contribute to safer, more efficient operations. Whether in hazardous locations or heavy-duty industrial settings, motor brake housings play an indispensable role in protecting both equipment and personnel.
2025-02-12 09:18:07
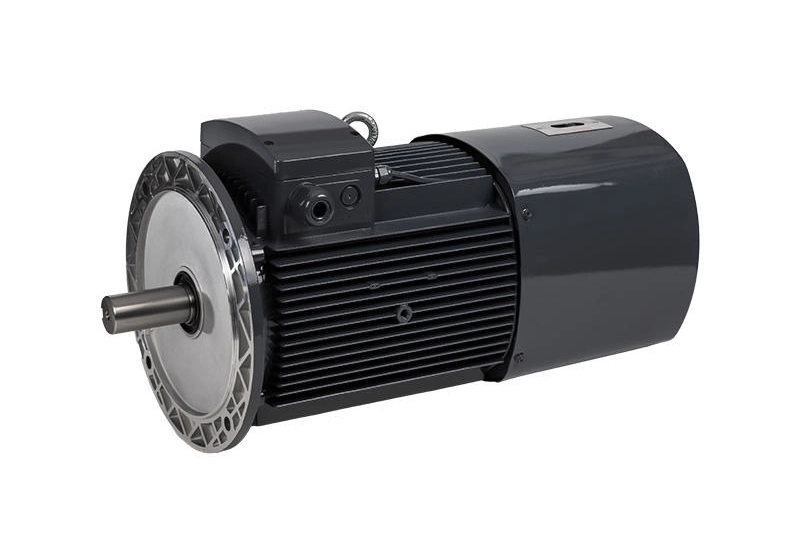
Motor brake housings might seem like a small component in a motor system, but their impact on the overall performance of motors is significant. These housings serve as the protective casing for the brake components, maintaining the integrity and proper functioning of the motor's braking system. A well-designed brake motor housing not only ensures the longevity of the motor but also directly influences its efficiency, safety, and operational stability. By providing structural support, reducing heat buildup, and protecting internal components, brake housings play a pivotal role in enhancing motor performance, making them a critical element in any motor-driven application.
2025-02-12 09:18:01
_1739257907682.webp)
Turbocharger impellers play a critical role in improving engine performance. By compressing and injecting air into the engine's cylinders, the impeller increases the amount of oxygen available for combustion, resulting in more power output. The impeller's efficiency directly impacts the turbocharger's ability to boost engine horsepower and torque. With advanced design and precision machining, such as those used by VIGOR INNO-TECH, turbocharger impellers are engineered to handle high temperatures, pressures, and corrosive environments. This ensures enhanced performance, durability, and longevity of the engine, even under extreme operating conditions. As the heart of a turbocharger, the impeller is essential for optimizing engine performance, fuel efficiency, and overall reliability.
2025-02-11 09:27:29
_1739257869423.webp)
The evolution of turbocharger impeller manufacturing has transformed dramatically over the years, driven by advancements in precision engineering and the demand for high-performance automotive components. At VIGOR INNO-TECH Limited, with over 18 years of experience in castings and forgings, we leverage cutting-edge technologies such as 5-axis machining centers to deliver high-quality turbocharger impellers efficiently. Through continuous process improvement, expert risk management, and precise quality control, we ensure that each impeller meets stringent performance criteria. Today, we'll explore the advanced manufacturing techniques that enable the production of turbocharger impellers that push the limits of durability, efficiency, and precision.
2025-02-11 09:27:20
_1739257835304.webp)
Turbocharger impellers are vital components in any turbocharged engine, playing a critical role in enhancing engine efficiency and performance. These impellers are subject to extreme conditions, including high temperatures and intense pressure. As a result, selecting the right material is crucial to ensure durability, performance, and longevity. In turbocharger impeller manufacturing, materials like Aluminum Alloys (Al-Alloy), Titanium Alloys (Ti-Alloy), and Stainless Steel are commonly used due to their exceptional mechanical properties, thermal resistance, and lightweight characteristics. Choosing the appropriate material depends on the specific requirements of the application, balancing factors like strength, weight, heat tolerance, and cost-effectiveness.
2025-02-11 09:27:10
_1739257407978.webp)
When it comes to high-performance brake camshafts, the choice of materials and manufacturing processes is crucial. A brake camshaft plays a vital role in converting the input force from the brake actuator into the rotational force that engages the brake shoes, ensuring your vehicle slows or stops effectively. At Vigor Inno-Tech, we combine expert material selection, precision die forging, and rigorous quality control to produce brake camshafts that deliver reliability and durability under demanding conditions. This article explores the key materials and processes that contribute to the development of high-performance brake camshafts.
2025-02-11 09:27:03
_1739257371855.webp)
When it comes to the safety of heavy-duty trucks and buses, brake camshafts play a pivotal role. These components are critical in the braking system, converting the force applied by the brake actuator into the rotational energy needed to engage the brake shoes. This process slows or stops the vehicle effectively, ensuring that large, heavy vehicles can come to a halt safely, even under demanding conditions. In industries where reliability and safety are paramount, high-quality brake camshafts are essential for preventing accidents and ensuring smooth, controlled braking in all situations.
2025-02-11 09:26:57
_1739257341614.webp)
When it comes to manufacturing brake camshafts, precision is everything. The tolerances involved in these components are critical to ensuring safety, performance, and durability in heavy-duty vehicles like trucks, buses, and trailers. Brake camshaft tolerances dictate how well the part fits and functions within the braking system, directly impacting stopping power, wear resistance, and overall operational reliability. For businesses relying on heavy machinery or transportation fleets, understanding the importance of precision manufacturing in brake camshafts can save costs, enhance safety, and boost long-term efficiency. In this blog, we'll explore the key aspects of brake camshaft tolerances, why they matter, and how precision manufacturing plays a pivotal role in delivering high-quality components for your business.
2025-02-11 09:26:50
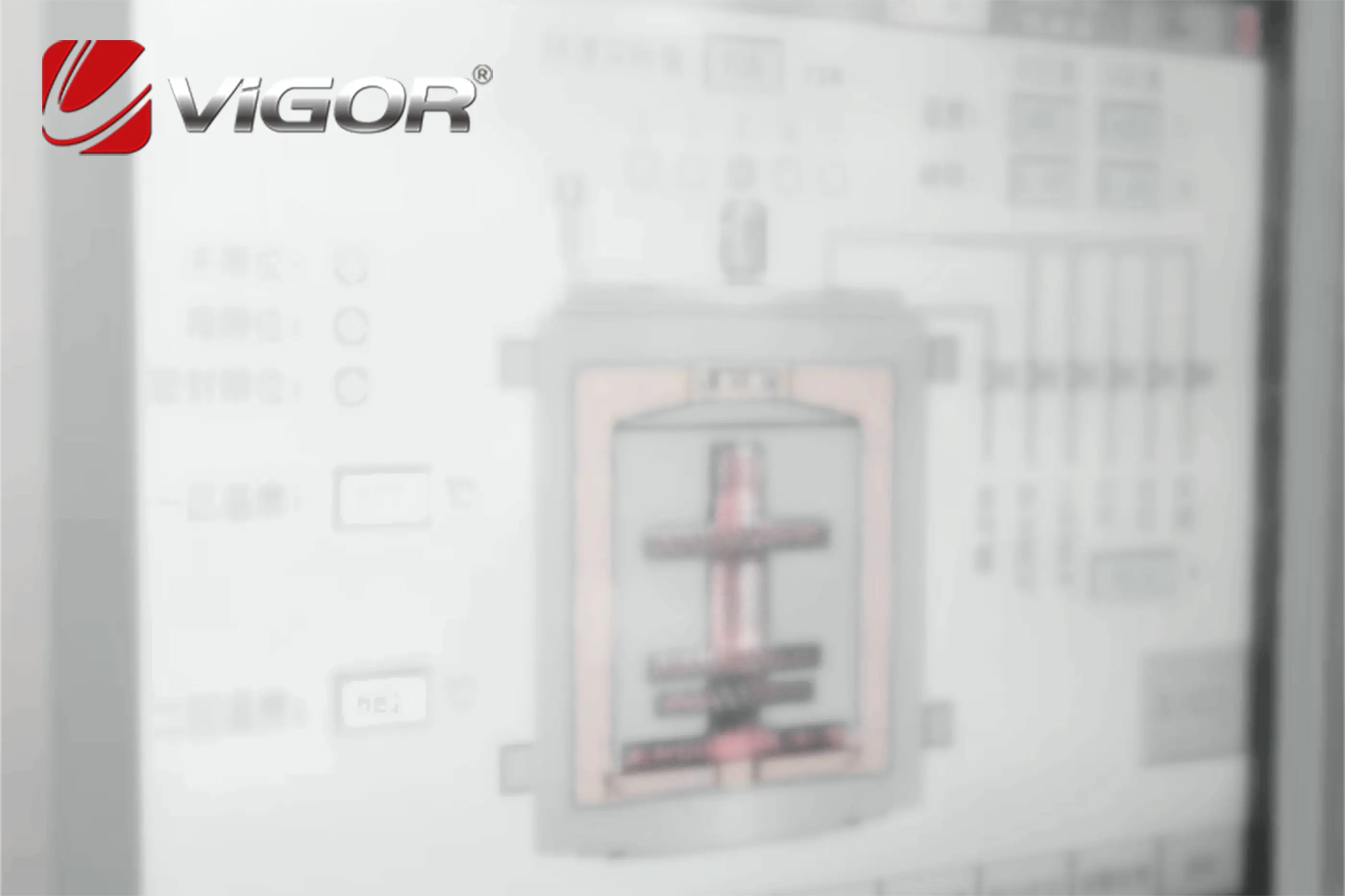
To prevent deformation of gear shafts during heat treatment, the following measures can be taken:
Preparation before heat treatment
Select appropriate gear shaft materials: Based on the working conditions and performance requirements of the gear shaft, choose steels with good hardenability and low deformation tendency. For example, for heavy-duty gear shafts, micro-deformation steel grades such as 18CrMnNiMoA can be selected.
Optimize gear shaft design: The design of the gear shaft should avoid complex shapes and uneven thickness as much as possible to reduce deformation caused by uneven internal stress distribution during heat treatment.
2025-02-08 16:02:22
131