
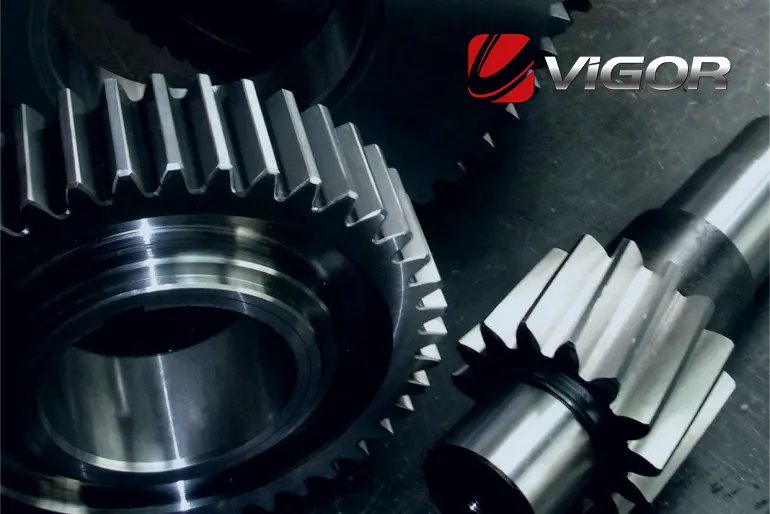
The differences and application environments between spur gears and helical gears
2025-02-08 15:55:13
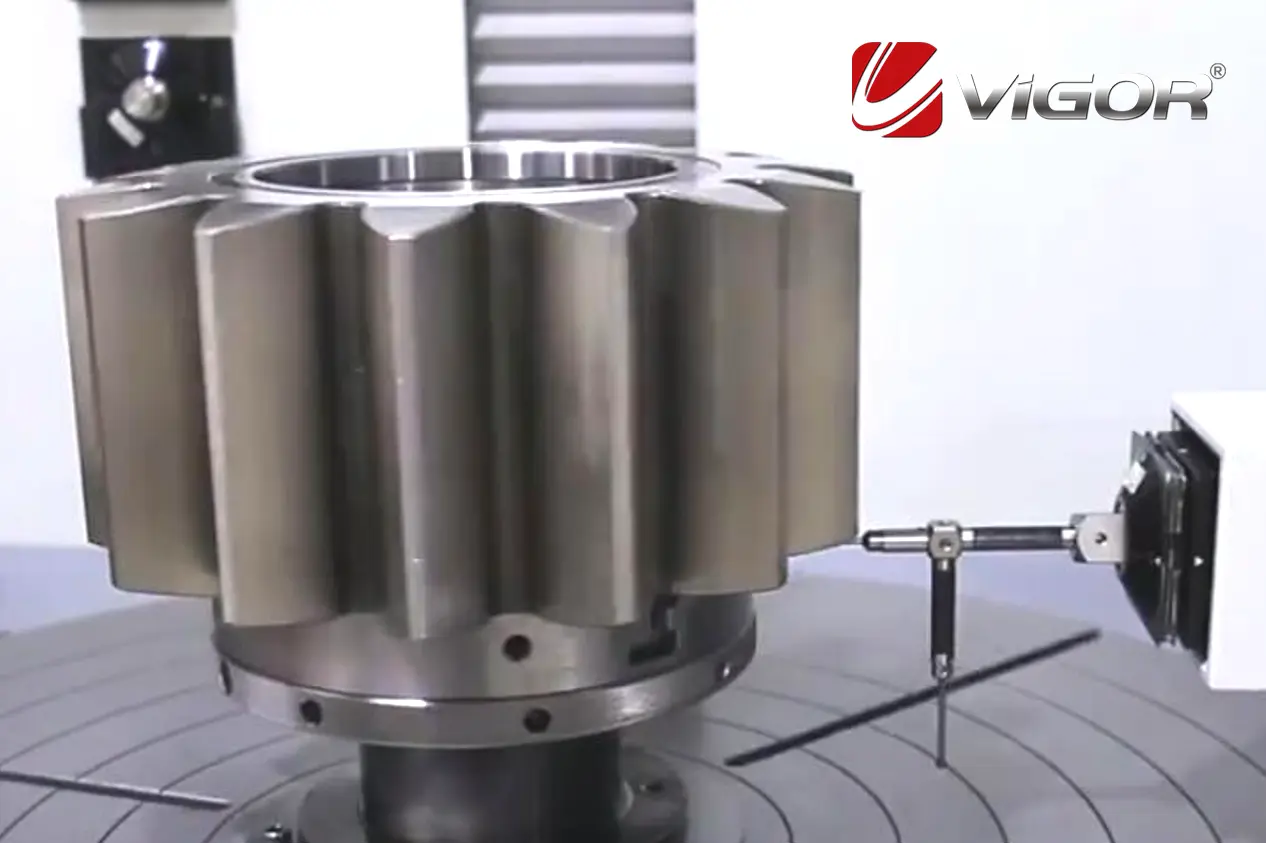
To reduce the noise of gear transmission, a multifaceted approach can be adopted to address various sources of noise generation. By focusing on design, materials, manufacturing, assembly, and operational aspects, significant improvements in noise reduction can be achieved. Below is an expanded discussion on each of these areas
2025-02-08 15:45:42
2025-02-08 09:29:14
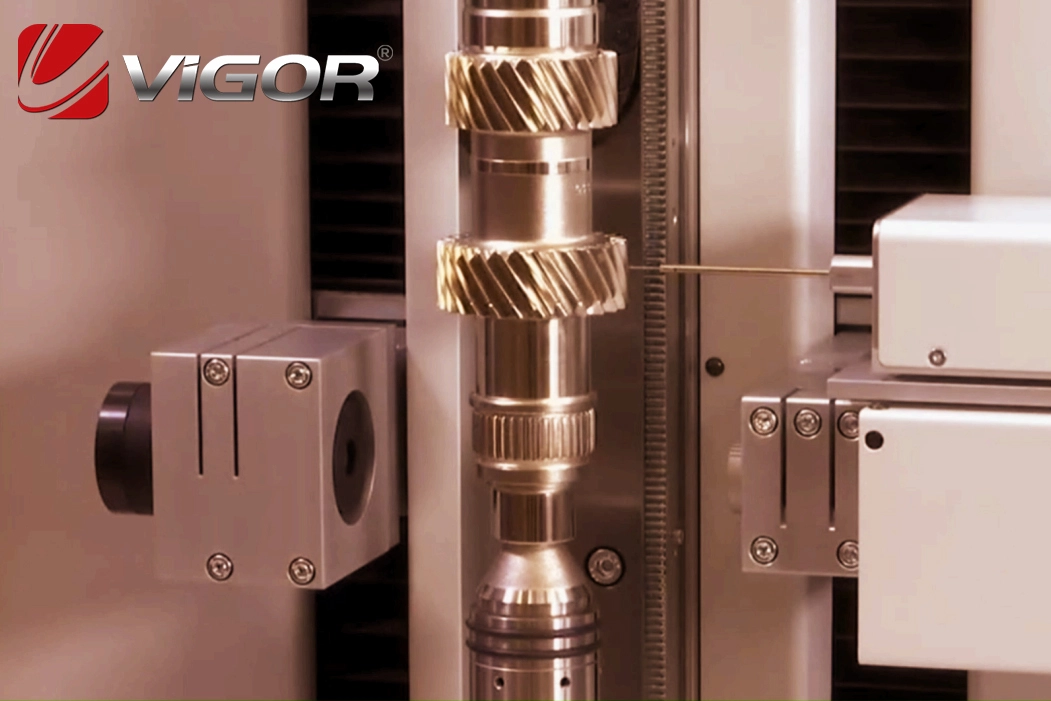
In the operation of various mechanical equipment, gear shafts, as key components of the transmission system, directly affect the overall efficiency and stability of the machinery. Different mechanical equipment have diverse working conditions and performance requirements, and conventional standard gear shafts are difficult to fully meet these needs. Therefore, customized gear shaft processing has emerged as a key solution to unlock higher transmission efficiency and more reliable working conditions.
Precise Customization to Meet Diverse Demands
Customized gear shaft processing can produce gear shafts with precise dimensions, materials, and precision based on the specific requirements of different equipment. From small electronic devices to large industrial machinery, Vigor Gear, with its professional technology and rich experience, tailors exclusive gear shafts for all types of equipment. For example, in the automotive manufacturing industry, gear shafts are customized according to the power requirements and transmission design of different vehicle models to ensure efficient and stable power transmission and a smooth driving experience.
2025-02-07 17:43:31
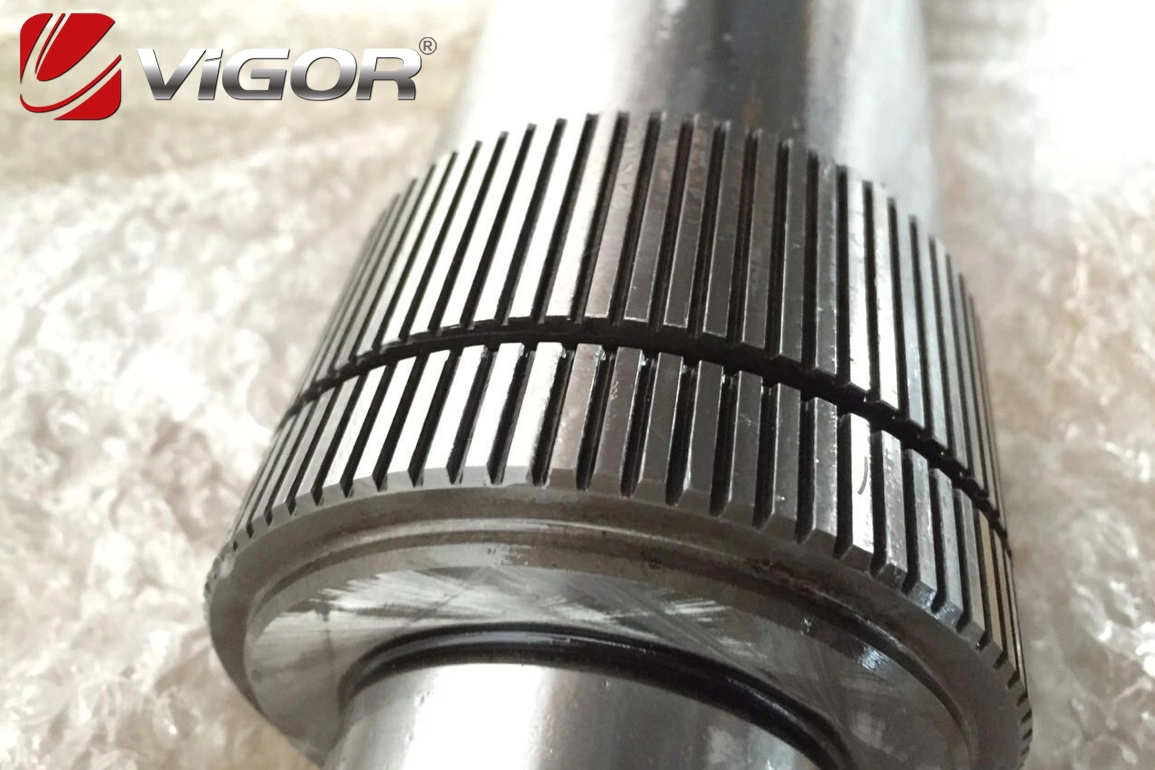
Selection of raw materials:
Suitable steel grades such as 40Cr and 20CrMnTi should be selected to ensure that the chemical composition and mechanical properties of the material meet the design requirements. At the same time, the appearance quality of the raw materials should be inspected to ensure there are no cracks, folds, or scars.
Precision of processing equipment:
The processing of splined shafts requires high-precision equipment such as milling machines and grinding machines. Regular maintenance and precision checks of the equipment should be carried out to ensure that all parameters are normal and prevent processing errors due to equipment precision degradation.
2025-02-07 17:42:27
In the vast landscape of industrial production, gear shafts are like the "central nervous system" of mechanical equipment. As core transmission components, the level of their processing technology is like a stabilizing anchor, profoundly influencing the efficiency of production and the quality of products. Advanced gear shaft processing technology is like a powerful engine, continuously providing impetus for efficient production in the industrial sector and has become a key force driving industrial progress.
High-precision processing ensures stable equipment operation
In the modern industrial production process, the high-precision operation of equipment is undoubtedly the key to ensuring product quality and production efficiency. CNC gear grinding technology, with its precise digital control, can finely grind the tooth profile of gears. Through computer programming, various grinding parameters are precisely set to achieve micron-level precision processing of the gear tooth surface, minimizing the tooth profile error. During high-speed operation, the meshing between gears becomes tighter and more stable, effectively reducing vibrations and noise caused by tooth profile deviations. Precision hobbing technology is no less impressive. It uses high-precision hobs to precisely cut the tooth profile on gear blanks. The manufacturing precision of the hobs is extremely high, with the shape and size errors of the cutting edges strictly controlled within a very small range. During the hobbing process, by precisely adjusting the relative position and motion parameters of the hob and the gear blank, high-precision gears can be processed, ensuring the accuracy and stability of the gears during transmission.
2025-02-07 17:41:09
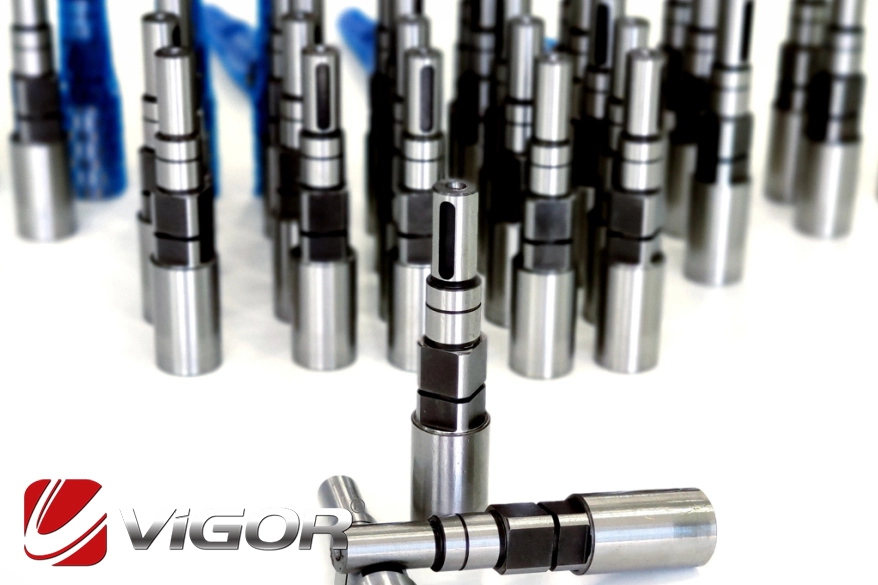
As a core component of the motor, the motor shaft has stringent performance requirements: it must possess high strength, excellent stiffness, and superior wear resistance to ensure stability during high-speed rotation while minimizing excessive heat generation and vibration. Therefore, when selecting materials for the motor shaft, the following aspects should be considered:
Microstructure and Grain Size: A finer microstructure with smaller grain size typically indicates higher strength and hardness, which can effectively mitigate the risk of fatigue and thermal fatigue fractures.
Heat Resistance: During high-speed rotation, friction can cause significant heat generation and increased surface temperature. It is essential to select materials that exhibit excellent high-temperature resistance and thermal fatigue performance.
Wear Resistance: High-speed rotation subjects the motor shaft to severe wear. Materials with higher hardness and superior wear resistance are necessary to withstand these conditions.
Machinability: Given the complex structure and precise processing requirements of the motor shaft, materials that are easy to machine and have good formability should be chosen.
Cost Considerations: Material selection should balance actual application needs with economic costs to ensure cost-effectiveness.
2025-02-07 14:12:44
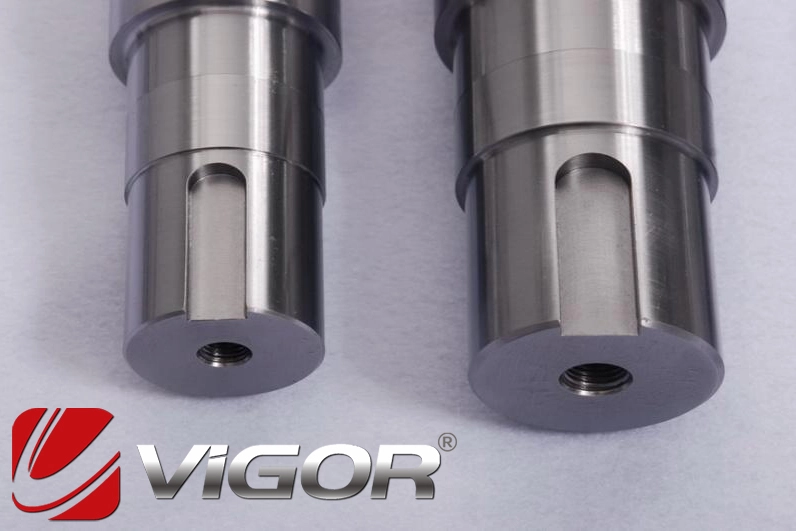
Motor shaft materials usually use high-strength alloy steel or stainless steel, while attention should be paid to the magnetic and precision requirements of the material.
Motor Shaft Material Type
There are various materials used for motor shafts, and different types of motors have specific requirements for the material properties. Generally, motor shaft materials can be categorized as follows:
High-strength alloy steel: Due to its superior wear resistance, corrosion resistance, and toughness, high-strength alloy steel is an ideal choice for motors with high-speed, high-load, and high-precision requirements.
Stainless steel: Characterized by corrosion resistance, heat resistance, and high strength, stainless steel is suitable for applications in marine engineering, petrochemicals, food industry, and other environments.
Cemented carbide: This material exhibits high strength, hardness, toughness, corrosion resistance, and wear resistance, making it appropriate for motors with high-load and high-precision requirements.
Copper-nickel alloy: With excellent heat resistance, corrosion resistance, wear resistance, and good electrical conductivity, copper-nickel alloy is well-suited for high-speed and high-load motors.
2025-02-07 14:04:59
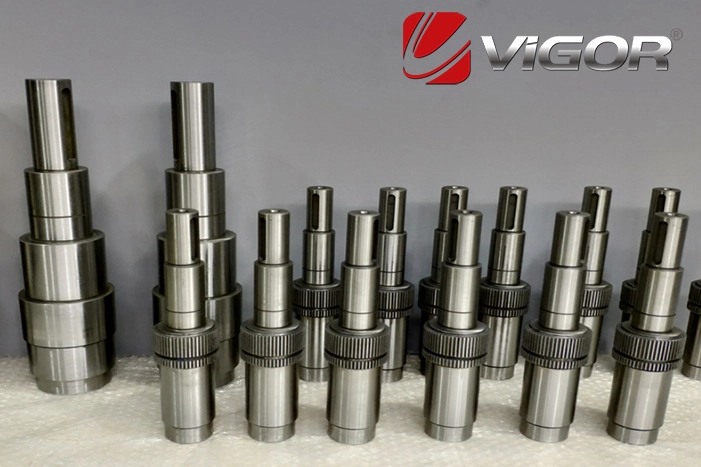
Spline shaft is a type of mechanical transmission component primarily utilized for the transfer of mechanical torque. It features longitudinal keyways on its surface, which align with corresponding keyways in the rotating components mounted on it, ensuring synchronous rotation. The following sections detail the applications, material selection criteria, and testing considerations for spline shafts.
Spline Shaft Applications
Spline shafts find extensive application across various mechanical systems, particularly where high torque transmission and precise control are essential. They play a critical role in industries such as aerospace, automotive, agricultural machinery, machine tool manufacturing, and general mechanical transmissions. Additionally, spline shafts are commonly employed in components requiring longitudinal sliding, such as transmission shift gears.
2025-02-07 14:02:18
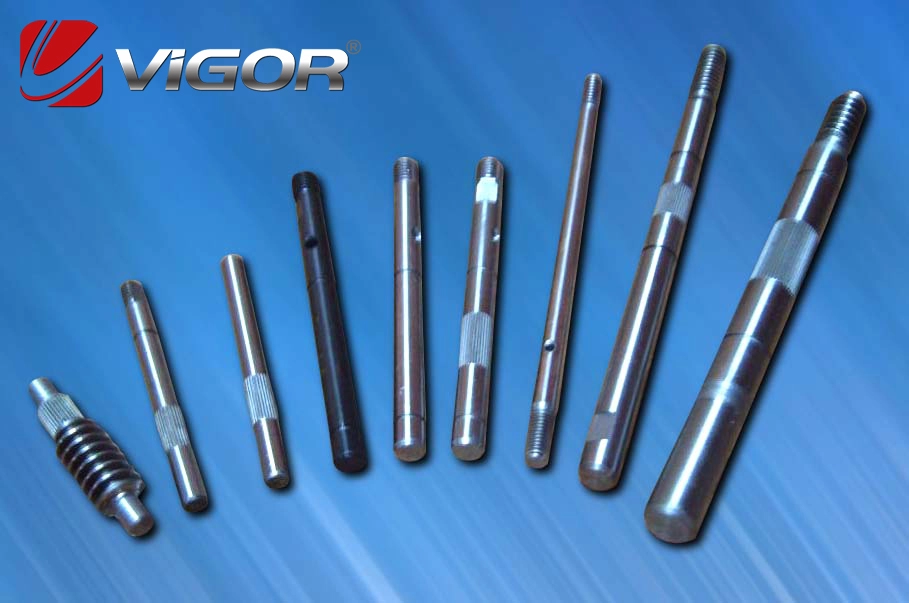
Wear and tear on motor shafts can lead to decreased performance, costly downtime, and even catastrophic failure if left unaddressed. Detecting wear and tear early is essential for maintaining optimal functionality and preventing unnecessary damage to your machinery. Common signs of wear include unusual vibrations, surface pitting, misalignment, or shaft corrosion. Regular inspections, precision measurements, and using advanced diagnostic tools are some of the most effective ways to monitor motor shafts and detect wear before it becomes a serious issue. By identifying the early indicators of damage, you can minimize risks and extend the life of your motor shafts, reducing repair costs and improving operational efficiency.
2025-02-07 13:47:32
131