
(1)_1735110334816.webp)
Sand casting is an age-old method known for its efficiency and versatility. The process starts with making a sand mold, which is then filled with metal to make it solidify. This technique is now popular in many industries. It is inexpensive, easy to use, and allows for the manufacture of complex parts. This paper will discuss sand casting in depth. It will describe its types, advantages and processes.
Its flexibility makes it ideal for casting metals ranging from a few grams to several tons in weight, such as iron, gold, lead and titanium. Different sands have higher melting points. They can make parts of all shapes and sizes.
2024-12-25 15:04:03
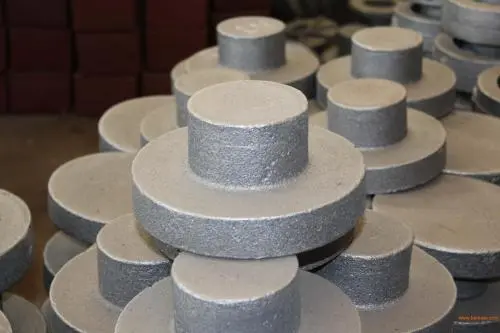
Sand casting is a casting method that produces castings in a sand mold. Steel, iron and most non-ferrous alloy castings are available sand casting method. As sand casting molding materials used in cheap and easy to get, casting manufacturing simple, single piece of casting production, batch production and mass production can be adapted to, for a long time, has been the basic process of casting production.
2024-12-25 15:00:35
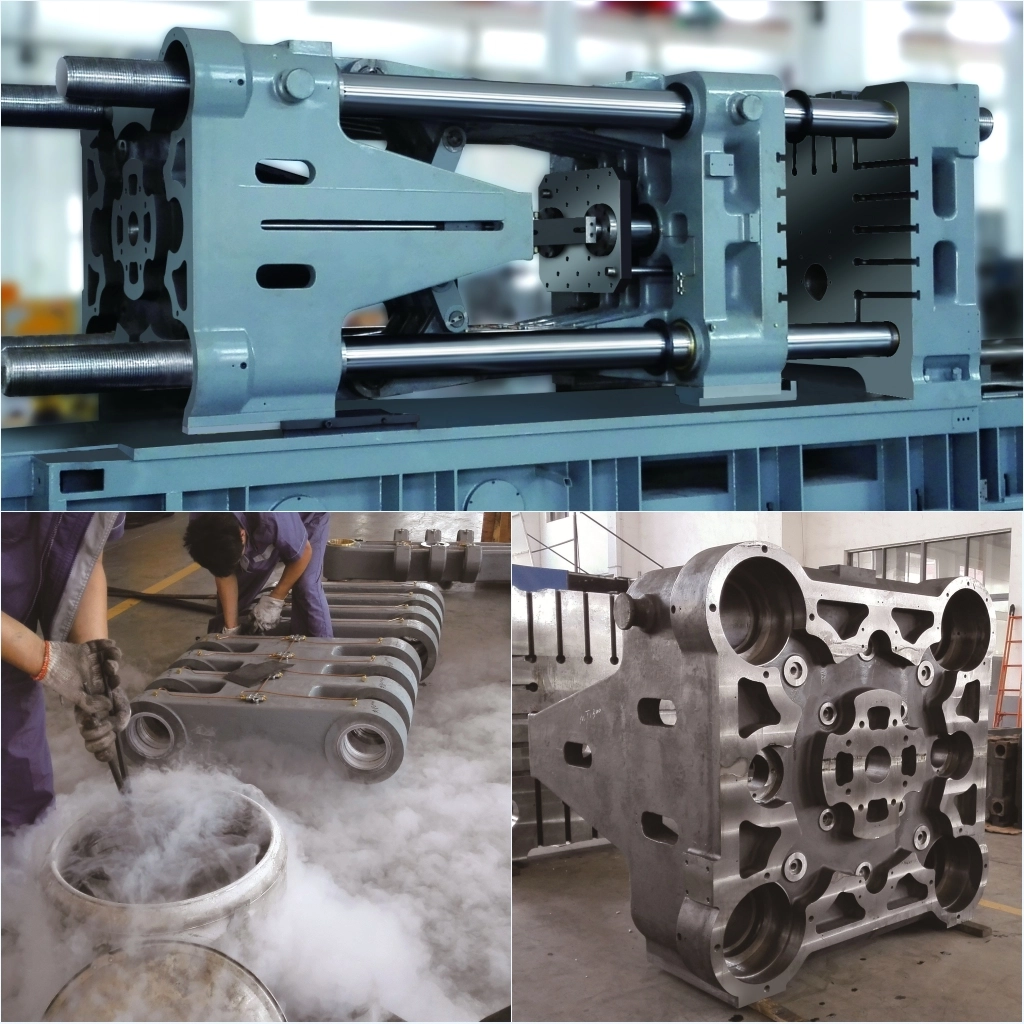
Cold chamber die casting is a widely used manufacturing process in the metal casting industry. It involves injecting molten metal under high pressure into a mold cavity, which is cooled to solidify the metal quickly. This process is particularly suitable for casting alloys with high melting points, such as aluminum, zinc, and magnesium. In this article, we will explore the various applications of cold chamber die casting and its benefits in different industries.
2024-12-25 14:58:22
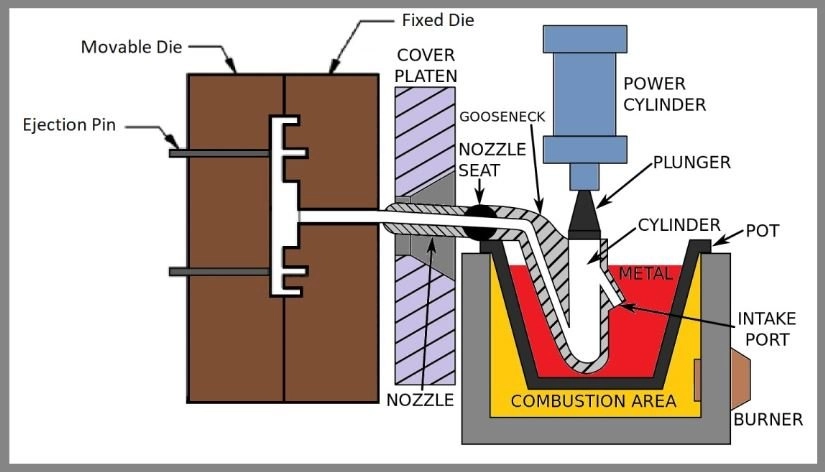
Hot chamber die casting is a precision casting process primarily used for producing small to medium-sized components made from non-ferrous metals, especially zinc, magnesium, and copper alloys. This process is characterized by its efficiency and cost-effectiveness, making it a preferred choice in various industries for manufacturing a wide range of products. In this article, we will delve into the applications of hot chamber die casting and its benefits in different sectors.
2024-12-25 14:56:31
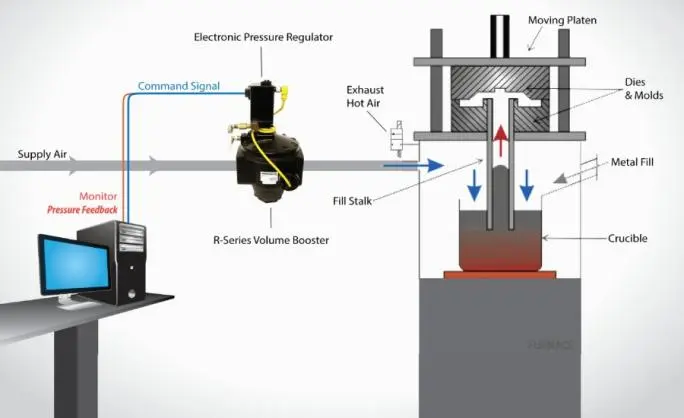
Low-pressure casting is a method of filling the cavity with liquid metal under pressure to form castings. In the casting process, the compressed air into the sealed crucible (containing liquid metal), so that the liquid metal surface by a certain gas pressure. Under the action of this pressure, the liquid metal along the rising liquid tube bottom-up through the gate smoothly into the casting cavity. When the liquid metal fills the cavity, the pressure is maintained for a certain period of time, so that the casting solidifies under the pressure, and then the pressure is lifted, so that the liquid metal that has not solidified in the ascending tube flows back into the crucible.
2024-12-23 16:40:22
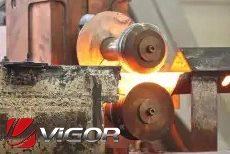
Investment casting, also known as lost wax casting, includes the processes of wax pressing, wax trimming, tree forming, slurry dipping, wax melting, metal casting and finishing. In lost wax casting, wax is used to make a wax mould of the parts to be cast, and then the wax mould is coated with slurry, which is the slurry mould. The clay moulds are dried and then baked to form ceramic moulds. After firing, all the wax moulds are melted and lost, leaving only the clay moulds. Generally, when the clay mould is made, the pouring hole is left open and the molten metal is poured through the pouring hole and after cooling, the required parts are made.
2024-12-23 16:38:11
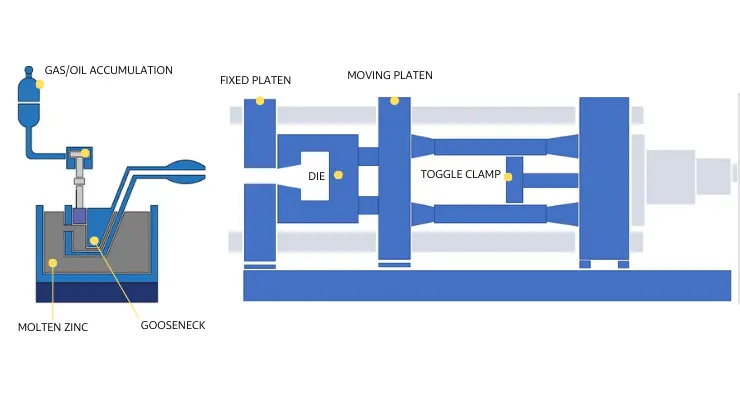
Hot chamber die casting is one of the most popular and widely used manufacturing processes in the world. This process involves the injection of molten metal into a die to create complex shapes, parts, and components. It is a highly efficient and cost-effective method that produces high-quality parts with excellent surface finishes. In this blog, we will discuss the advantages and disadvantages of hot chamber die casting.
2024-12-12 17:49:25
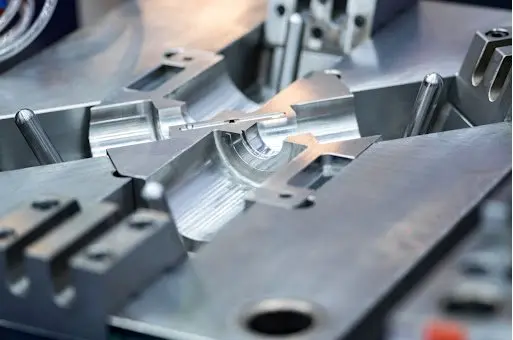
Cold chamber die casting is a prominent manufacturing process used across various industries to create metal parts with high precision and quality. Unlike the hot chamber process, the cold chamber method involves injecting molten metal into a die that is separate from the injection chamber or cylinder, which does not come into direct contact with the molten metal. The process is known for its efficiency, enabling rapid production of large quantities of parts. However, it's not without its challenges and limitations.
2024-12-12 17:42:04
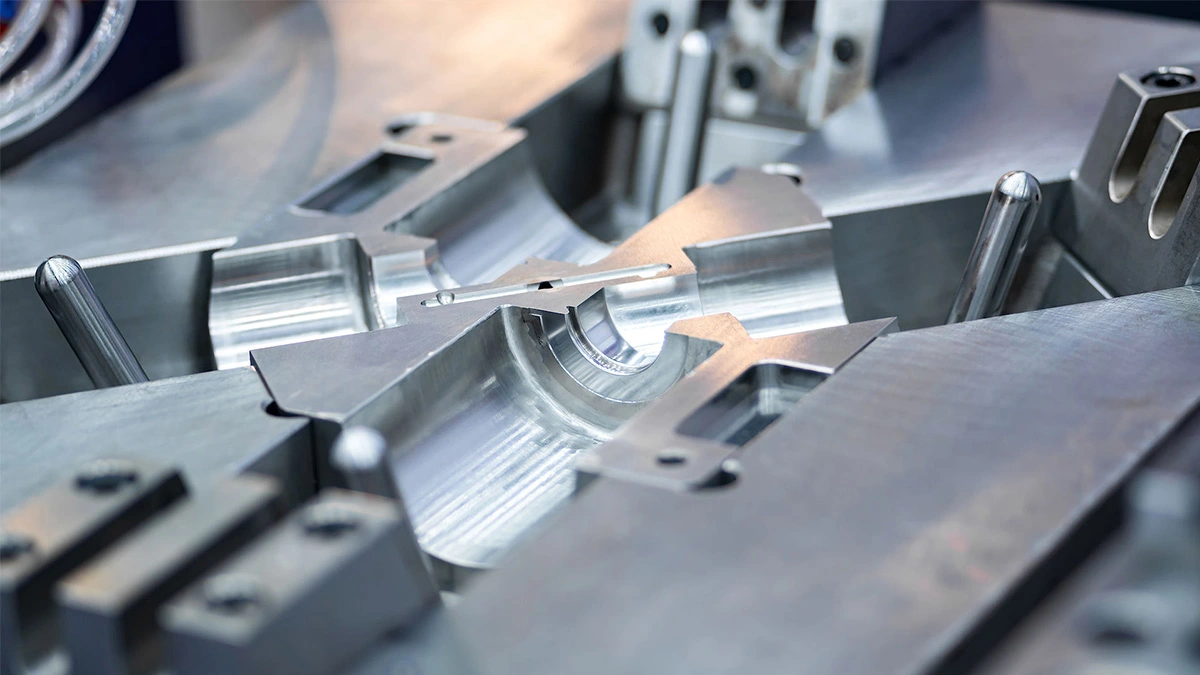
In the modern manufacturing industry, the accuracy and performance of metal parts are increasingly required, and squeeze casting technology has emerged as a bridge connecting the advantages of casting and forging. This technology, with its unique process flow and excellent product characteristics, has brought revolutionary changes to the field of metal processing.
The basic process of squeezing die casting includes preheating the mold, injecting liquid metal, applying pressure, and curing and cooling. This process not only improves the heat flow rate, but also eliminates macroscopic and microscopic shrinkage pores, while limiting pore formation due to dissolved gases in the molten metal
2024-12-11 17:08:56
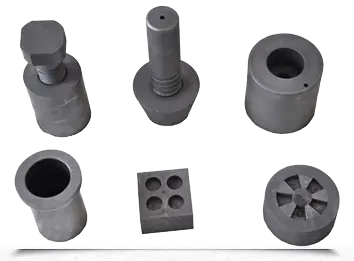
In the pursuit of industrial efficiency and material properties today, continuous casting technology has become a leader in the production of steel and non-ferrous metal preform with its outstanding advantages. This technology, after more than a century of development and improvement, has become an indispensable part of the metal materials industry.
2024-12-11 17:06:29
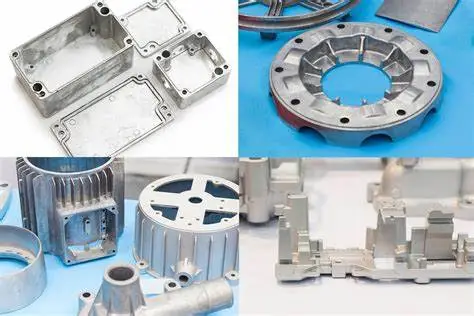
2024-12-05 13:48:55
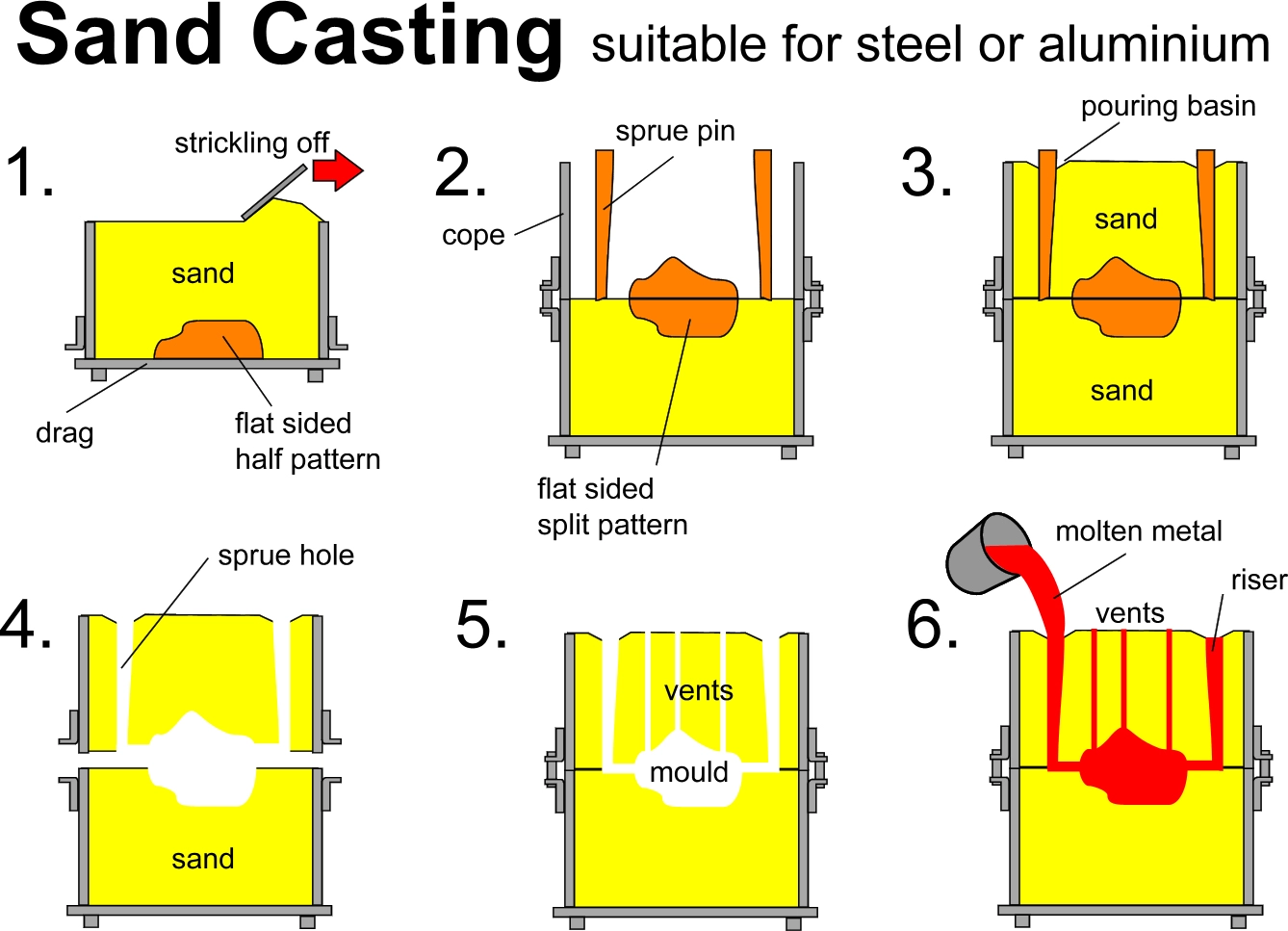
Casting process is a metal hot working process, which involves melting the metal into a liquid state and then pouring it into a pre-prepared mold (mold), allowing it to cool, solidify, and finally form a casting with a certain shape, size and properties. Casting process is an important method of metal forming, which is widely used in industrial production, especially in the manufacture of large, complex or metal parts with specific performance requirements.
2024-12-05 13:11:10
131